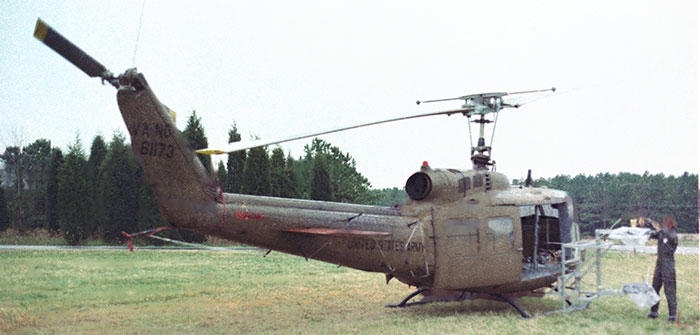
Jammer Testing with Helicopters
February 01, 2018
By Stuart Moran
Special Guest Writer
In the early 1970s we were testing high-power electromagnetic pulses to see if they could be used as weapons against enemy electronics. We constructed various devices that produced pulses of nearly a million volts to connect to homemade antennas. We always had difficulty measuring exactly what these homemade systems would produce and radiate. Our group built underground trailers to house the high-voltage systems under a large wire grid laid on the ground, which served as an ideal conducting ground plane. Measurements were made at some distance (in the far field) and compared to theory. We decided to suspend magnetic field sensors below helicopters to get above the ground effects. A photo was shown in the previous blog on the early days of RF.
Much of the early high-power pulse testing showed how difficult it was to permanently destroy distant electronics. Temporarily disrupting them was much easier, so we got the idea to run the devices at a fast repetition rate to create jamming effects. We began testing a family of spark gap jammers that were lower voltage but ran at thousands of pulses per second. The idea was to drop these on parachutes over the enemy to jam communications, radar, and data links during a strike. Again, measuring the radiated output away from ground effects was difficult, so we again turned to helicopters.
One day of testing was particularly memorable. One of the members of our group was a former Vietnam helicopter pilot and a member of the National Guard. He obtained a helicopter and co-pilot in Richmond and flew to Dahlgren, landing between the cedar trees and the power lines behind our trailers, located in the then-isolated area where Building 1490 now stands (see figures 1 and 2). These helicopters had clip-latches on the sides to attach stretchers for use in medical evacuations. We designed a framework to attach to these latches that could hold our jammers, power supplies, and antenna structures. After the helicopter landed, we bolted the system on, loaded the instrumentation and scope cameras, and were off (see figures 3, 4, and 5). On the ground were crews to receive the jammer signals and also some enemy-like receivers being tested for effects.
We headed out over the Potomac River and performed some close-range tests over the water to make sure everything was working before heading out over Maryland at higher altitude. The noise energy from the jammers caused the master caution light to come on, which made the pilots very nervous, so we had to make sure this was truly a false alarm before we could proceed. For the actual testing, we wanted to simulate a parachute drop at useful ranges, so the idea was to hover at several distances and make measurements. I learned that hovering at high altitude is a very difficult thing for a helicopter to do, since there is no ground effect. If you are not careful, the rotor wash can sort of self-circulate and you lose control. We had a few eye-opening moments, but the pilot was very capable.
Since the system we had bolted on was rather heavy, and on one side, the pilot was compensating with his control stick to keep the craft level. After considerable testing many miles over Maryland, it became obvious that as the heavy fuel was being consumed, the problem was getting worse, and his control stick was almost all the way to its limit. Finally he said, “We need to get more fuel before I lose control.”
And we headed toward the air station at Patuxent River. Unfortunately, on the way we hit the limit of the stick and we heard the pilot radio he had to land immediately.
“Is this an emergency landing?”
“No, just precautionary.” We dropped abruptly into a cornfield somewhere in southern Maryland.
My partner and I quickly jumped out and unbolted the framework, power supplies, and gas bottles, and pulled everything away from the helicopter as it lifted off before it ran out of fuel, and the pilot headed out.
My partner and I looked at each other. We were standing in the middle of a large field of brown corn wearing stripped flight helmets, flight suits, life jackets (in case we ditched in the river), and safety straps that had been tied to the helicopter in case we fell out of the open doors. We were standing beside a collection of aluminum frames, electronics, and homemade antennas with a few tools in our hands. We had no radio or any means of communication. Off in the distance, on a hill was a farmhouse, and several people had come out to see what all the commotion was about. Someone got into a truck and started toward us but then turned around and went back. There was nothing we could do but stand there and wait. After about a half-hour we started wondering if the pilot even knew where he left us.
We finally saw the helicopter on the horizon going past us and we realized he couldn’t remember where we were. We had flares with us, but there had been a drought, and with the dry corn around us we did not want to risk a fire. Finally, after several distant circles, we were spotted. This time we loaded the equipment into the center. Just after liftoff we dropped back down. The pilot smelled smoke—very bad for a helicopter. It turned out a strap buckle had fallen across the top of one of the equipment batteries and caused the plastic top to catch fire. We quickly extinguished it with our gloves, and proceeded back to the base.
The test was successful and we got good data. There was a very simple solution to the balancing problem. We built two framework/jammer assemblies, one for each side (see Figure 6). The helicopter had no trouble lifting the weight; it was the one-sided twist that was the problem. We used this two-sided approach on subsequent testing of this technology at other bases and never had another problem.
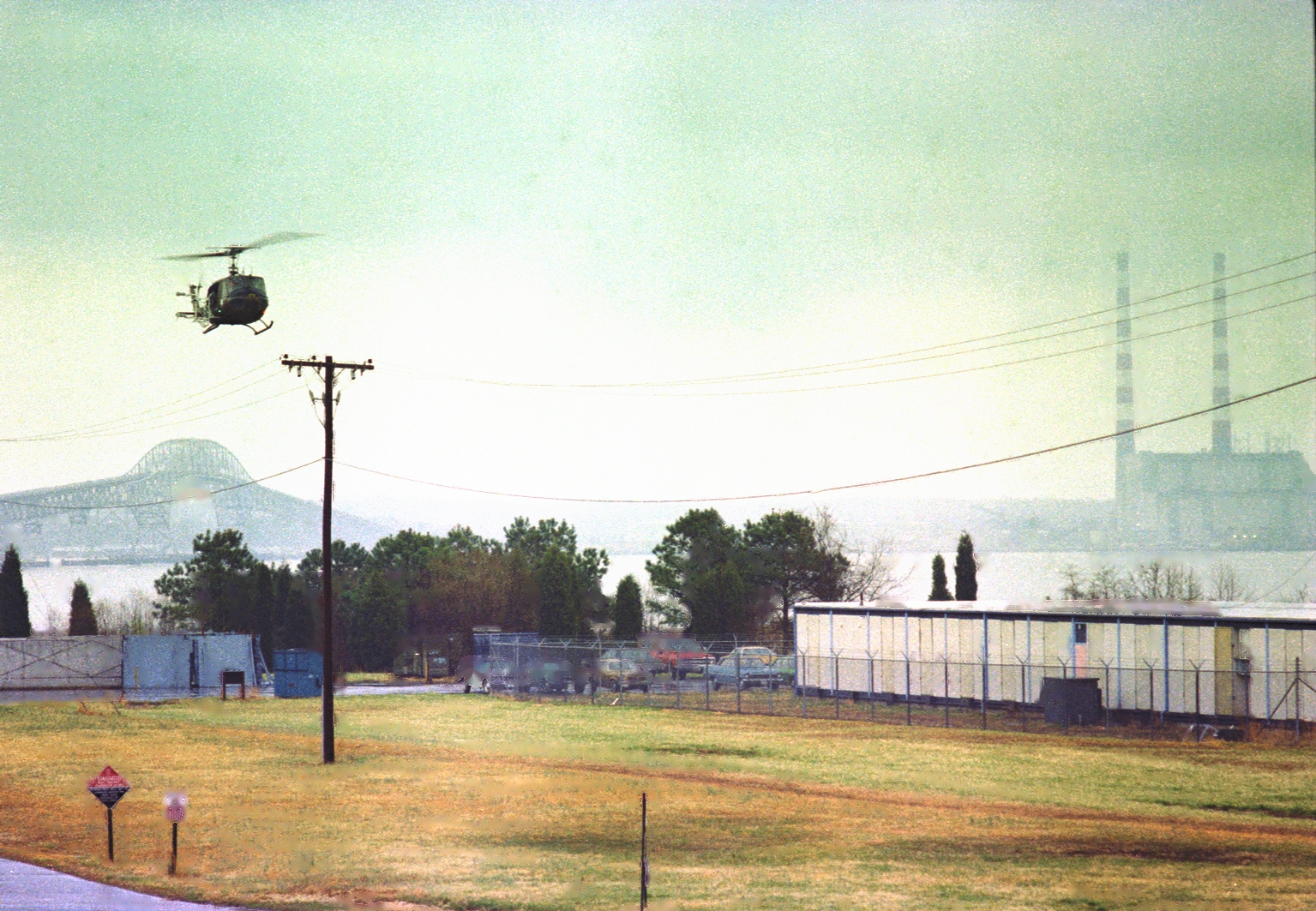
Figure 1. Helicopter landing by the 424 trailer complex. Note bridge and power plant.
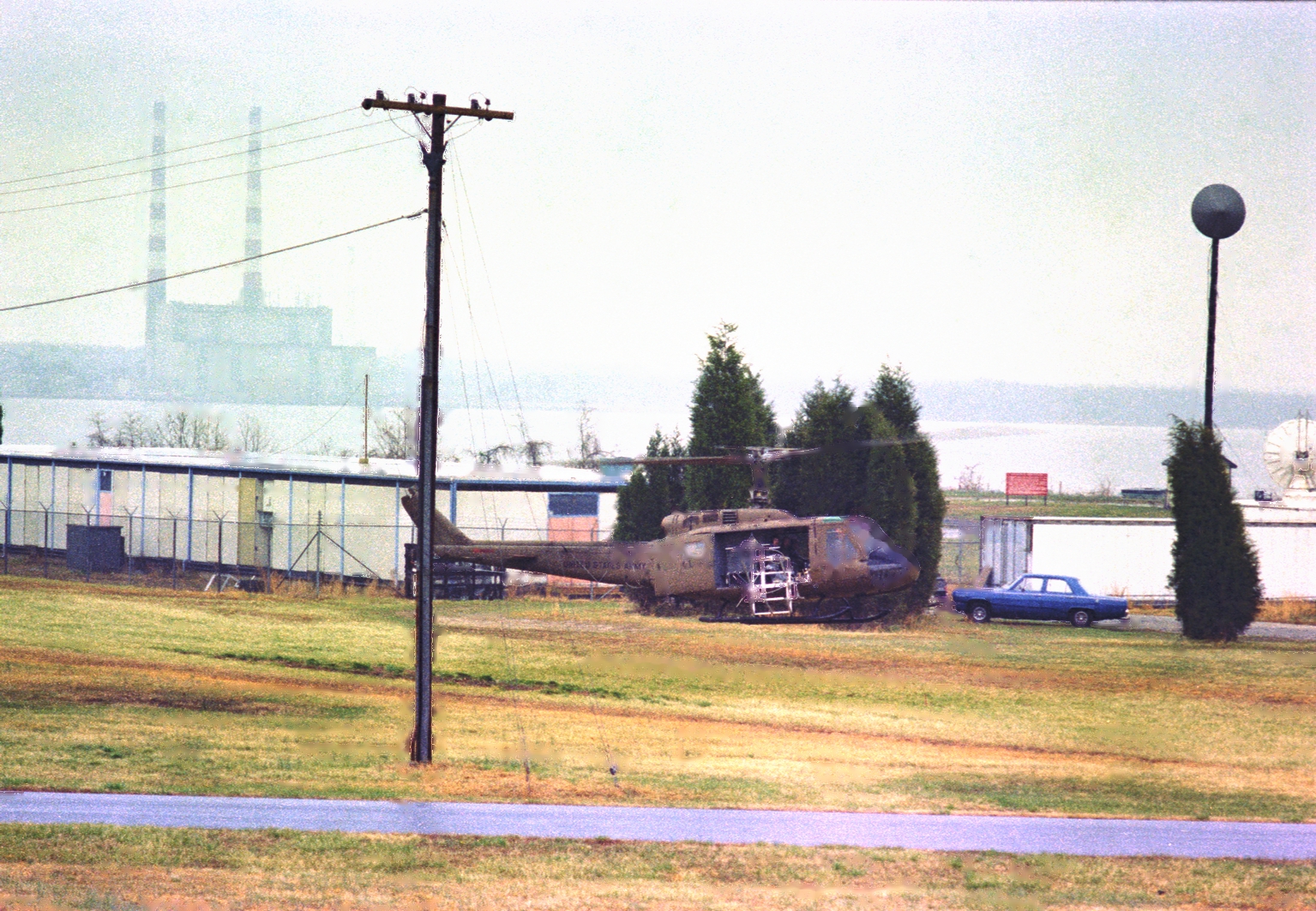
Figure 2. Helicopter taking off from behind 424, the present location of Building 1490. The 1975 microwave tower communicated with an anechoic chamber a half-mile away (Building 1400).
.jpg?ver=2018-01-24-144831-030)
Figure 3. Stuart Moran and Larry Rinehart beside the jammer framework attached to the helicopter.
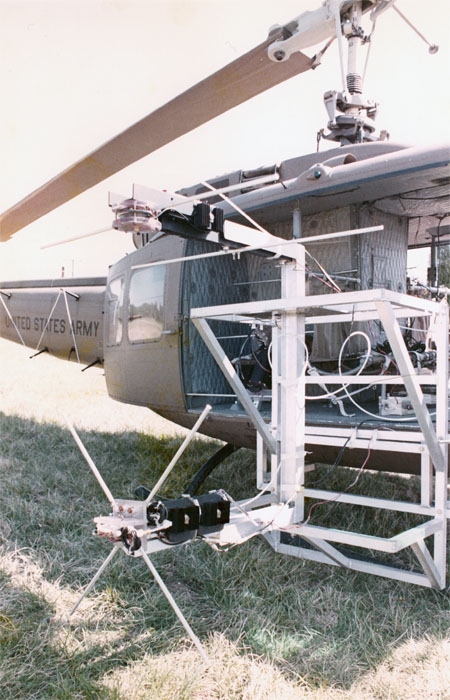
Figure 4. Jammer Framework attached to one side of the helicopter.
.jpg?ver=2018-01-24-144831-043)
Frame 5. Stuart Moran making last-minute changes to the jammers before takeoff.
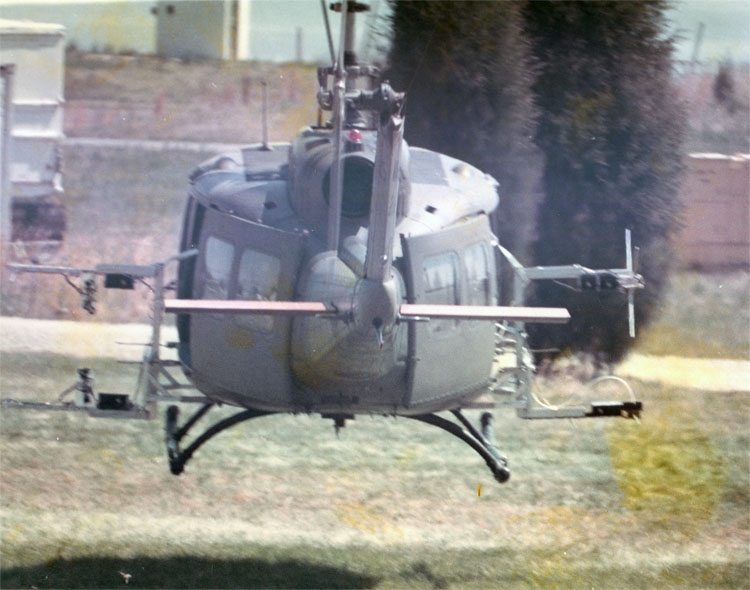
Figure 6. Follow-up design placing equal weight on both sides of the helicopter.