Armor and Projectile Laboratory
December 4, 2017
Dahlgren is known today as a center for research and development, but that wasn’t always the case. From its founding until just before World War II, much of the work concentrated on testing ordnance. Research and development was a marked departure from the status quo. One of the earliest ventures was the Armor and Projectile Laboratory. Today’s blog post outlines its history and achievements.
The laboratory was the brainchild of Dr. L.T.E. Thompson, previously of Clark University, who became Chief Physicist at Dahlgren in 1923. Conventionally, the Navy depended on steel manufacturers to ensure the quality of steel used in armor and projectiles. The quality of the armor had proved inconsistent, so Thompson and Experimental Officer William “Deak” Parsons believed the field required some metallurgical research. The research capability was limited then because there were no available facilities or personnel to conduct the required experimental tests. Additionally, “an armor piercing projectile, by definition, had to be a major caliber projectile,” and conducting research with large guns was too expensive.
Therefore, Thompson and Parsons wanted a laboratory where they could conduct all testing at a smaller scale and produce results that could be scaled up and applied to the larger guns. Thompson later recalled he was “able to justify a proposal for a research laboratory at reduced scale, the point being that if you could get most of the information with very small scale, say 1, 2, 3 inches, 4 inches diameter projectiles, you could get ahead much faster,” and the testing would be more cost effective. For reference, the 3-inch projectiles would be scaled down from 60-inch projectiles. They knew that because the experimentation would concern the properties of the metal itself, most of it could be conducted with smaller projectiles and armor and still remain valid when it was scaled up for usage.
Thompson submitted his proposal for the laboratory, but the entire concept of it was politically controversial within the Bureau of Ordnance (BUORD), which had the power to accept or block the proposal. The BUORD consulted steel experts on the need for such a laboratory, but the experts were employed by steel manufacturing companies and were disinclined to encourage research that could have results contrary to their company’s interest. The proposal stalled, but was eventually approved and granted a Congressional appropriation of $300,000 when Admiral Bowen of the Naval Research Laboratory threatened to take over the work.
|
A&P Lab Building |
In February 1941, Thompson brought in Leonard Loeb, a naval reservist and physicist with the University of California at Berkeley. Loeb’s first task was to oversee the construction of a building to house the laboratory. It initially consisted of a single building, which, “was actually forward of the main battery line… So the place had to be built with no windows at all, completely closed up.” It had an armor-plated tunnel for firing guns up to 3 inches and laboratory space that a later history reported as containing capabilities for heat-treating metal; fabricating projectiles; gauging; mechanical testing; metallographic, chemical, and physical analyses; radiography; woodworking; bulge testing; fragment testing; and drafting.
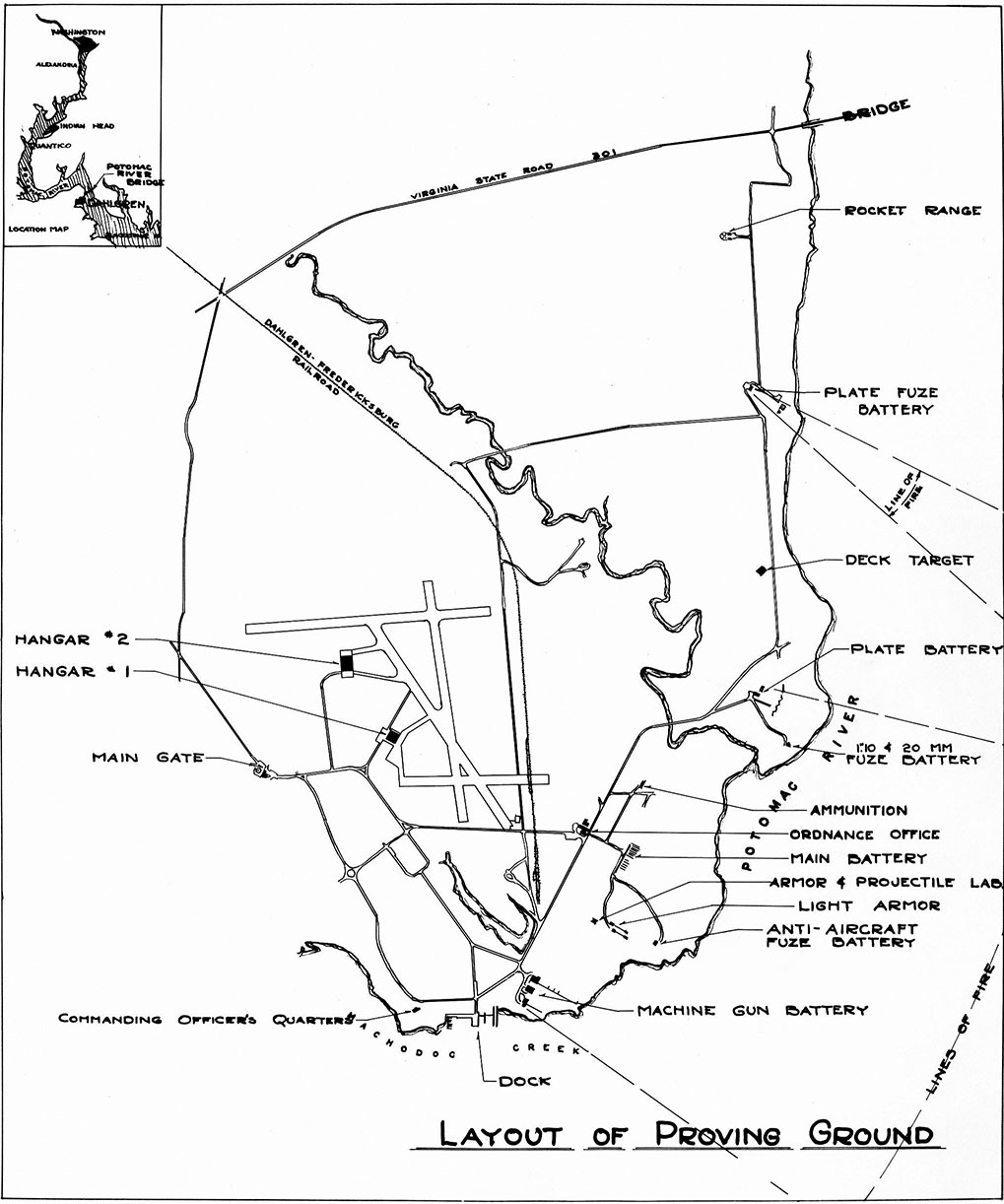
|
Map of Dahlgren showing the location
of
the A&P Lab Building |
Loeb’s other task was to recruit “a strong staff of physicists, chemists, and metallurgists.” Loeb’s philosophy in staffing shaped the lab’s future because he realized “that there was a big gap between the scientist in the laboratory and the officer in the field, and [he] felt that no scientist was in the position to help the Navy unless he knew the Navy.” Thompson, Parsons, and Loeb—all scientists with an academic background—were also all naval officers, so Loeb staffed the laboratory with naval officers. Conveniently for him, while at the University of California, “he got a lot of his physics students into the reserves,” and was then able to hire them to staff the laboratory. 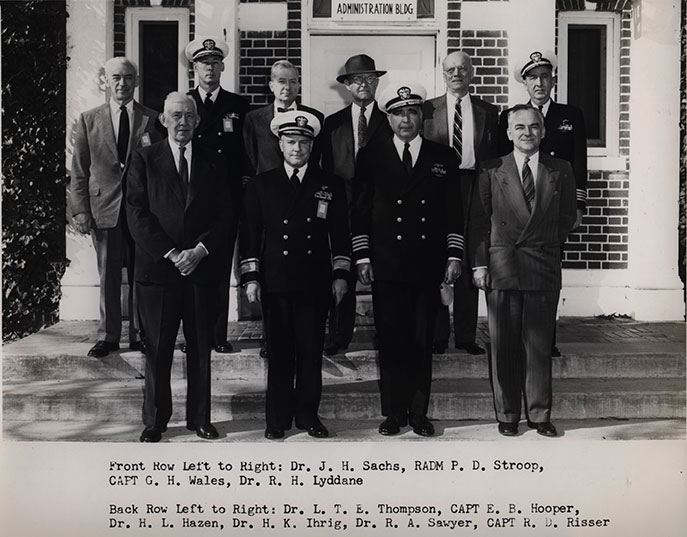
Institutional changes, however, brought difficulty to the lab. A change of command in April 1941 saw the installation of Captain David I. Hedrick, whose vision for Dahlgren did not include the Armor & Projectile Laboratory. Ralph Sawyer, a spectroscopist and one of Loeb’s former students who came to work in the lab, recalled that Hedrick ”felt really that this was a proof and test place and that they were to test ammunition , projectiles, and armor and not to do research work.” According to historians James P. Rife and Rodney P. Carlisle in The Sound of Freedom, “Hedrick’s contempt for Thompson’s experimental research program in general, and the new A & P Laboratory in particular, brought the tensions to a head…. Hedrick moved to disband the laboratory and drive out Thompson.” Hedrick attempted to destroy the laboratory through attrition, blocking acquisitions and reassigning much of the staff to other positions at Dahlgren.
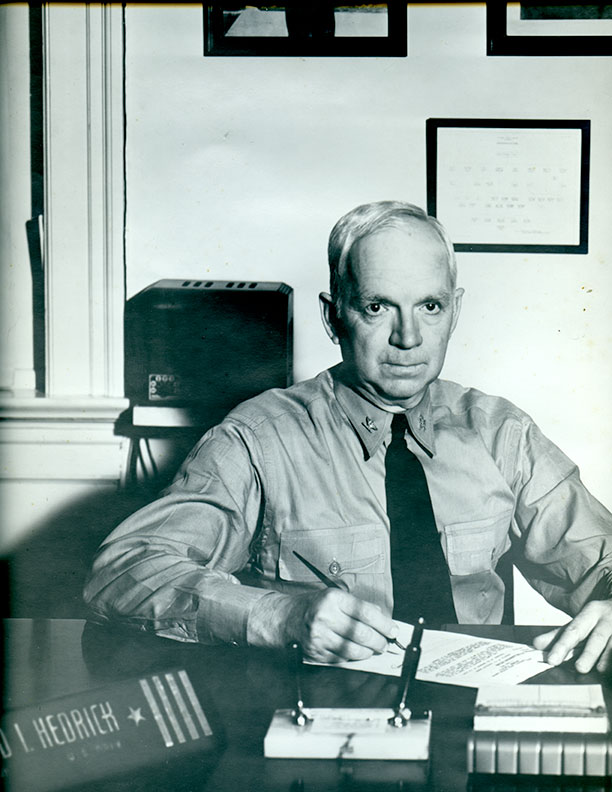 |
CAPT David I. Hedrick |
Thompson and Loeb both left Dahlgren as a result of Hedrick’s obstruction. Loeb became so frustrated with Hedrick that he requested to be removed from active duty and return to his job at Berkley. He attempted to convince Hedrick that his job in creating the laboratory was done, and because there was no staff and no substantial work could be accomplished, it was best to let him leave. Hedrick was reluctant, but “then finally it was conveyed to him that there was a little black book,” Loeb kept as a record of Hedrick’s wrongdoings, “and there might be a court of inquiry.” Loeb effectively blackmailed Hedrick and was able to return to the university in August. Thompson also left the lab within the first months of U.S. involvement in World War II. Loeb claimed he had left after attempting to oust Hedrick, but Thompson did not corroborate that story. When Sawyer returned to active duty in February, 1942, he was the de facto head of the laboratory.
Although Thompson’s idea for the laboratory predated World War II, the earliest work they conducted was directly related to the war. Robert Varney, a physicist working in the laboratory, recalled that “following the Battle of France in 1940, US army observers returned to the US bugged eye with the news that army 75 mm field artillery pieces could not penetrate German tank armor. Dr. Thompson was able to tell the army ordnance department that he already had a 3-inch armor piercing projectile in production,” which was very close in size, so they modified their equipment and began testing 75mm projectiles to learn how to improve their hardness.
|
75 mm projectile |
The beginning of U.S. involvement in WWII brought with it a new demand for metallurgical testing of armor and projectiles. The laboratory, however, bled of staff and funding, was in no shape to conduct the research. Hedrick’s efforts to suppress research went so far as to prevent the visiting director of the British National Physical Laboratory from seeing the Armor & Projectile Laboratory, a move that eventually backfired on him. “After returning to Britain, [he] wrote a blistering report on the sad state of American armor research for Winston Churchill,” which snowballed into directions from President Roosevelt “to go ahead full blast.” The laboratory’s staff returned to their work.
The war necessitated the continuation of work because “there was a continual battle development between better armor and better projectiles.” Armor and projectiles needed to be produced at ever-increasing quality and in greater quantities. Adding to the need was the fact that, during the war, companies that usually focused on other products began producing armor. Their lack of experience making armor meant they made mistakes that compromised its quality. The laboratory was uniquely equipped to deal with those problems because they “were able to heat treat armor up to 5” thick and 3 or 4 feet in diameter across. So that [they] were able to make more tests than the armor makers… [they] were able to make big improvements... and find out what was wrong with the armor that they were making.”
The improvements they made mostly concentrated in increasing the hardness of armor. Samples of armor the Navy was going to use were sent to the laboratory for testing before it was implemented. Robert Varney, a physicist with the lab, gave one particular example of testing armor for planes in explaining how their process worked during the war. He said they tested it with scaled-down armor piercing projectiles but the hardness was insufficient and it failed the tests. They then attempted to solve the problem. “We took single pieces of the aircraft armor and re-heat treated them in our beautiful, precisely controllable electric furnaces. The very same pieces of armor that were being penetrated by .50 caliber projectiles at 1500 feet per second velocity prior to re-heat treating now stopped the same projectiles at 2500 feet per second.” When the laboratory’s metallurgists visited steel production facilities to determine why the armor was not meeting hardness requirements, they found that the inexperienced companies were packing too many plates of armor into their furnaces; as a result, the armor was not heating evenly. Ralph Sawyer felt that gaining knowledge of the properties of homogeneous light armor and developing the process of case hardening were the laboratory’s greatest achievements during the war.
The laboratory also applied its methods for testing armor and projectiles to gathering information about enemy armor and projectiles. The lab saw many examples of armor and projectiles the American fleet recovered and sent back to the United States for “intensive metallurgical examination and analysis.” Instances of this process are recorded in technical reports written by the lab after the examinations, and the reports exemplify the lab’s expertise. One of these cases was a Japanese 8-inch projectile recovered from USS Salt Lake City. Its fragments were shipped to the Armor & Projectile Laboratory, and there were cut into sections for testing. The sections allowed lab personnel to discover “the design of this projectile seems excellent for conventional use against lightly armored targets; however there is the possibility that this projectile may also have been designed for use against heavily armored vessels by underwater attack of their light armor. In such an attack the windshield is ripped off, thus also removing the cap and transforming this capped projectile into a flat nosed projectile.”
|
Photograph showing how the A&P Lab assembled the slices
of the projectile and the resulting drawing of the projectile |
Despite the laboratory’s clear wartime benefit to the Navy, the end of the war presented new challenges to incorporate it into normal operations. Ralph Sawyer “felt the place was going to shrink in volume pretty fast… they intended to let most of the reserves go and everybody was leaving.” Sawyer himself left in 1946. According to his successor, Russell Lyddane,
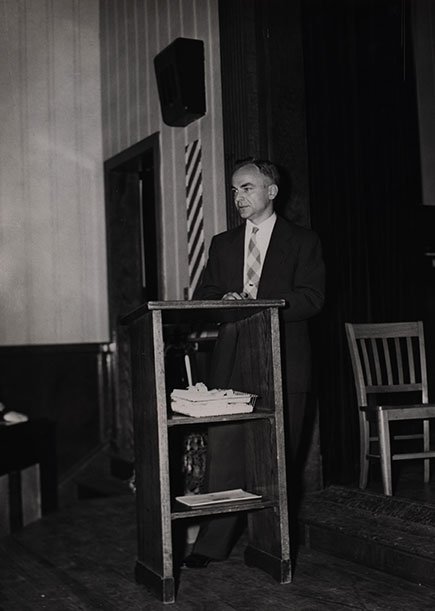 |
Russell Lyddane |
the laboratory’s vision was to hire more civilians and forge a place for itself in the new post-war environment, because they did not believe the Dahlgren Proving Ground would survive if it only conducted proof and test instead of becoming more involved in research and development. It also “didn’t have a stake in the R & D that was going to go on again in the ’50s when the missile programs started and began absorbing large sums of money.” Within the next few years, the Terminal Ballistics Department formed with the intention of making bombs, rockets, and warheads. The Armor & Projectile Laboratory became the laboratory component of the department with a mission that paralleled Thompson’s original ideas: “To improve projectiles (including bombs, rocket heads, and missile warheads) and armor by correlating mechanical, physical, chemical, and metallurgical studies with ballistic results.”