Download the PDF file
INTRODUCTION
The
DMSMS is defined in Department of Defense Material Management Regulation
4140.1-R as, “the loss of, or impending loss of, the last known supplier of an
item or raw materials. DMSMS occurs when
manufacturers of items or raw material suppliers discontinue production due to
reasons such as rapid change in item or material technology, uneconomical
production requirements, foreign source competition, Federal environmental or
safety requirements, or limited availability of items and raw materials used in
the manufacturing process. DMSMS situations tend to have a pervasive effect that
not only precludes repair of materiel but also precludes procurement of
additional systems, equipment, spare assemblies, and subassemblies that depend
on the DMSMS items and raw materials for their manufacture.” It means that the last known supplier or
manufacturer will no longer produce a particular item. This document is intended
to provide assistance in management of Diminishing Manufacturing Sources and
Material Shortages (DMSMS).
BACKGROUND
DMSMS is a problem that has been confronting
program managers, logisticians, and item managers in both the Department of
Defense (DoD) and private industry, for more than twenty years. Almost anything
can become a DMSMS item, including electronics, connectors, racks, motors,
valves, adhesives, switches, circuit breakers, propellers, metal alloys, ceramic
composites, gases, clothing or its various components and materials, etc. DMSMS is a potential showstopper. It can prevent aircraft from flying, ships
from sailing, and tanks from deploying.
DMSMS cases may occur at any phase in the acquisition cycle, from design
and development through post-production, and have the potential to severely
impact weapon system supportability and life cycle costs. The majority of DMSMS cases have historically
been in the electronics area (primarily microcircuits); however, DMSMS problems
affect all weapon systems and material categories. DMSMS problems are not always confined to
piece parts. Material obsolescence
situations may occur at the part, module, component, equipment, or other system
indenture level. Obsolete parts can be
mistakenly designed into new systems every day.
Obsolescence is also very expensive, costing the U.S. military hundreds
of millions of dollars each year.
A number of factors contribute to cause DMSMS (Figure 1). The prime driver of DMSMS
situations is the commercial profit motive; when a part is no longer economical
to produce, manufacturers will shut down product lines and move on to more
profitable items. Manufacturers end
production of older items and begin production of new items to stay on the
leading edge of technology and maintain their competitive edge. A product market may be too small to be
profitable. A combination of both DoD and industry driven factors has created
the magnitude of the DMSMS problem existing today. The new emphasis by the DoD to use
commercial
rather than military standard parts,
has caused some manufacturers to cease production of all military standard
parts. From a manufacturer perspective,
rapidly changing technologies, increased foreign competition, federal
environmental and safety regulations, and/or limited availability of materials
may make continued manufacture of selected items uneconomical or otherwise
unattractive. DoD procurement practices
further compound the problem (Figure 2).
Long design to acquisition lead-times, as well as increasing service life
extension of programs, mean that support requirements for military systems
generally extend from 25 to 30 years, as opposed to the 4 to 7 year support
cycle expected for many commercial electronic systems. In addition, in many cases the military
percentage of total commercial demand has dropped sharply. In the early 1960s, the U.S.
Government’s procurement of integrated circuits (ICs) accounted for
approximately 95% of the market, and is less than 2% today. This combination of extended support periods and
diminished overall demand has left military systems highly susceptible to DMSMS
problems.
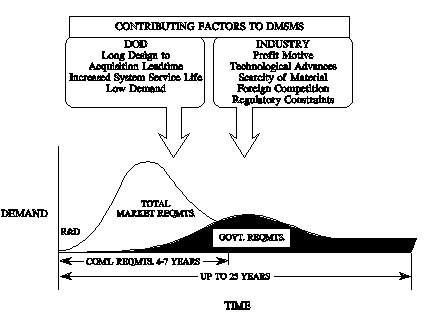 |
Source: DMS Case Resolution
Guide
|
Figure 1. Contributing Factors to DMSMS
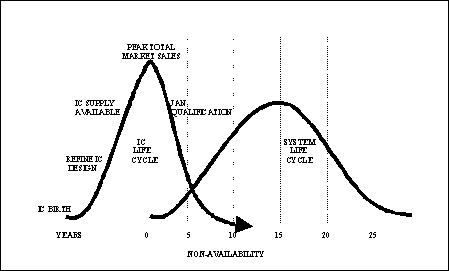 |
Source: ICE |
Figure 2.
IC/System Life Cycle
Even after DMSMS situations are
identified, resolution efforts are often hampered by a number of factors,
including: short notification response timeframes, which leave insufficient time
for the DoD to review options in end of production cases; lack of coordination
among impacted parties (both government and industry), which affects development
of cost-effective resolutions; and lack of dedicated DMSMS funding, which means
that dollars from other program areas must be found to resolve obsolescence
issues. At the same time, if cognizant
systems/equipment were not provisioned to the piece part or microcircuit level,
or if provisioning data is incomplete/inaccurate, it may be difficult or
infeasible to cross DMSMS part numbers to specific system
applications.
GENERAL
GUIDANCE
The
selection and application of parts to meet the performance requirements of the
system or equipment are very important in DMS management. To assure meeting those objectives, it is
recommended to have parts engineering processes and procedures in place. The following is list of some primary area of
concerns in device selection.
IC Products Technology Selection And Trends
The IC
industry is often looked upon to introduce new and innovative devices. Ever-increasing electrical and technological
advances necessitate that new products enter the market. As new products are introduced to the
marketplace, existing components are pushed further along their lifecycle
patterns.
In general, the introduction-position
IC is an upgrade in circuit density over existing parts. Although
introduction-type ICs receive most of the trade press publicity, the IC
manufacturer makes the majority of its money on ICs in their growth and maturity
stages. However, because of the
competitive nature of the marketplace and the need to acquire production
experience (to move down the learning curve), it has proven very difficult to
enter a market segment in the “profitable” stages without having had a part
available in the introduction stage.
The IC industry has historically
introduced or described products well before the time that the devices were
ready for commercial mass production.
While some of the advances tout device or process enhancements or unique
design methods, it usually takes some time before most introductory products are
embraced by the IC industry. The underlying causes of this typically slow
acceptance of new ICs are high initial costs, existing infrastructures, and
oftentimes, user concerns about the quality and reliability of the new
technology or products.
Military ICs are typically one to two
lifecycle stages behind commercial ICs (Figures 3,
4). Because of long lifecycles of
many military electronic systems, ensuring a consistent supply of hi-rel
ICs has
been a demanding task.
As IC manufacturers concentrate capital
resources and Research & Development (R&D) efforts on commercial ICs in
the early part of their lifecycles, less support will be given to devices in the
saturation and decline stages. This
situation becomes especially serious for military IC users when an IC part type
that is in the maturity stage of the military lifecycle is also in the decline
stage of the commercial IC lifecycle.
The following two figures represent the 1998
status of commercial and military IC lifecycles. In selection of parts, it is generally
recommended to avoid those IC products in Introduction, Saturation, and Decline
(Obsolete) stages of the IC Lifecycle curves.
It is recommended to selects parts from Growth and Maturity stages where
these parts are free of initial problems, readily available through multiple
sources, and have moderate cost.
The electronics industry is being driven by the commercial
marketplace for higher speeds and more efficient power management leading to
lower voltage operation in higher density components. Five-volt (5-V) electronic
systems have been the industry standard for active devices such as
microcircuits, diodes and transistors for the last several decades. However, due
to processing advancement in device design; 3-V, 2-V, and 1-V have emerged as
the new low power technology. The trend in the electronics industry going
towards these lower operating voltages will impact Navy system acquisition and
sustainment. The trend indicates that
there will be less and less of 5V market for all new design as time goes by and
it will be harder to sustain old legacy systems. Long-term strategic DMSMS planning is needed
for better management of the upcoming technology transition issues.
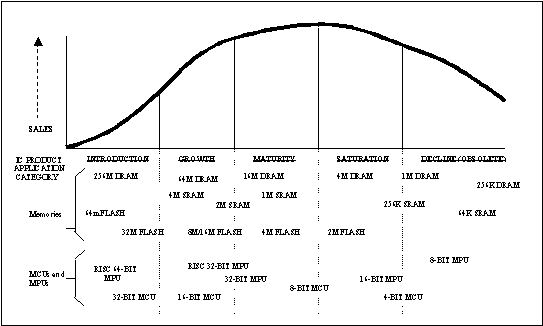 |
Source:
ICE |
Figure 3.
Commercial - IC Lifecycle
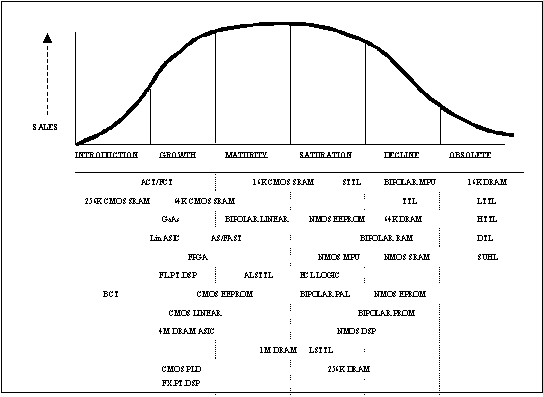 |
Source:
TI |
Figure 4.
Military - IC Lifecycle
Order Of Preference In Parts Selection
In general, the following are the order of
preference in parts selections (in the descending order):.
a.
Parts required to meet Government regulatory organization’s
regulations.
b.
Parts
defined by standards produced by recognized national consensus standard
societies and organizations.
c.
Military
or Government standard parts.
d.
OEM
corporate standard type parts.
e.
Source
control drawings or vendor item drawings.
f.
Parts identified by part manufacturer part numbers, which are controlled
by their drawings, catalogs, or company standards.
Source Selection
Considerations
The DMS task could be applicable to all options, and the
Acquisition Activity (AA) must decide if the period of expected use,
criticality, and cost of the hardware to be purchased warrant a DMS task. The
following statement of work (SOW) is suggested for guidance.
“The contractor shall review, through the period
of performance of the contract, the Government/Industry Data Exchange Program
(GIDEP) Diminishing Manufacturing Source (DMS) notices and other supplier
notifications for applicability of the hardware being delivered. The contractor shall notify the Acquisition
Activity within ____ days of any DMS situation that effects current deliveries
or subsequently will effect equipment maintenance and repair (data item number
for notification of DMS problems).”
Optional Task: “Through the period of
performance of the contract, the contractor shall: (1) Identify alternate
sources, replacement parts, or optional part numbers for
parts and materials that become obsolete, and (2) revise the assembly drawings
to incorporate the new information. If a
direct replacement is not possible, the contractor shall notify the Acquisition
Activity.”
The acquisition
activity (AA) or designated representative would need to review the contractor’s
proposed parts management plan or internal parts management procedures for the
following criteria.
Parts Management Criteria
To better manage the selection and use of parts to reduce
life-cycle cost and to avoid unnecessary proliferation of part types, procedure
is recommended to:
a.
Define
the parts selection process or criteria, including an order of preference.
b.
Establish
the parts evaluation and authorization processes.
c.
Use and maintain an approved corporate baseline, parts selection list, or
other database to give visibility to designers and subcontractors of parts
preferred for use.
d.
Manage
subcontractors.
Parts Quality and Availability
To ensure part quality, enhance equipment/system
reliability and supportability, and reduce DMS occurrence, the contractor should
have provision for:
a.
Assessing
parts suppliers and their technology roadmaps.
b.
Documenting
and maintaining part failure information.
c.
Using
Government Industry Data Exchange program (GIDEP) data.
d.
Using
DMS information databases.
e.
Enhancing competitive re-procurement of spares.
LIFE
CYCLE SUPPORT
Provisions must be made to
ensure system support throughout its life cycle. Programs must use information
sources and processes to alleviate the DMSMS issues that will occur.
Discontinuance
Notifications
Initial DMSMS alerts may be promulgated by a
variety of sources, subsequent to manufacturer discontinuance of part or a line
of products. Alerts may also be
originated when Navy activities receive a “no bid” on parts orders for
manufacturing components, or a “not available” response to a depot requisition
for repair orders or the manufacturing of parts. Part manufacturers and OEMs generally provide
discontinuance information directly to major government and commercial
customers; in addition, a variety of internal government systems have been
established to distribute DMSMS alert data.
The following is a summary of the primary DMSMS alert sources.
Part Manufacturers and OEMs
Discontinuance notifications are often received from part
manufacturers and OEMs via letter or telephone call. In both cases,
manufacturers will generally notify only known customers of the part or
component in question. If the government
is not a direct purchaser of the material, discontinuance information must then
be passed through suppliers and OEMs who are under contract
to government activities. For example,
alerts may be originated by OEMs when a component manufacturing contract cannot
be filled because a supplier has provided them a discontinuance notice on a part
needed for a contracted component. To
ensure receipt of such notifications, NAVSEA programs should insert appropriate
requirements and clauses in system support and production contracts.
Government Procurement/Repair Activities
Internal government alerts may be generated subsequent to "no
bid" or "not available" responses to equipment or part procurement/repair
efforts. In these cases, a technical
referral has historically been generated and forwarded on a Defense Logistics
Agency (DLA) Form 339 to an Inventory Control Point (ICP), which may pass the
information to an in-service Engineering Agent (ISEA) for further review and
analysis. Contact with ICP/ISEA
technical referral personnel may therefore be necessary to obtain specific alert
information.
Inventory Control Points (ICP)
ICP DMSMS alerts may be promulgated in the course of part
application reviews during ICP case research.
The center will generally provide impacted activities with problem part
numbers, end item application data, and the case number via telephone.
Government-Industry
Data Exchange Program (GIDEP)
These alerts originate when GIDEP is notified by a part
manufacturer or GIDEP participant that a part or production line will be
discontinued. GIDEP promulgates alerts
to representatives at subscriber activities in DoD, and to member organizations
in private industry. These alerts
sometimes duplicate DESC or DTC information as discussed below, and normally
contain data such as the last date of part manufacture, last date for order
processing, and minimum order quantity or buy value.
Defense Supply Center Columbus (DSCC)
DSCC alerts are received by naval message and generally identify
a DMSMS problem with a fairly immediate response requirement. They generally request identification of
quantities required for Life-of-Type (LOT) support, and submission of funded
requisitions and/or Military Interdepartmental Purchase Requests (MIPRs) for
hardware to be acquired for subsequent use in new higher assemblies. These alerts usually have a short lead-time
for response and are frequently promulgated before research to identify
alternate sources of supply can be completed.
DMS Technology Center (DTC)
The DTC, located at Naval Surface Warfare Center (NSWC) Crane,
Indiana provides DMSMS alerts via the Internet and Rapid Alert Notifications
(RAN) via E-mails.
Monitoring Technology
To mitigate DMSMS risks in a
configuration item, you must first know the parts and their indentured
relationship in that item. Upon receipt of a discontinuation
notification, research has to be conducted to verify if the DMSMS situation
exists or not. Therefore, it is very
important to maintain an accurate and comprehensive baseline configuration. The
following are some of the primary products, which may be useful for obtaining
configuration data.
·
Management
Data List-Consolidated (ML-C)
·
Management
List, Navy (MLN)
·
Master
Cross Reference List (MCRL)
·
Consolidated
History of Alternate Identification Numbers (CHAIN)
·
Master
Repairable Items List (MRIL)
·
Identification
List (IL)
·
Federal
Item Logistics Data Record (FILDR)
·
Master
Index of Allowance Part Lists (APLs)/Allowance Equipage Lists (AELs)
·
Navy
Activity Specific Databases
·
Original Equipment Manufacturers Systems.
Resolutions
The following list of resolutions, are not
necessarily mutually exclusive; the potential may exist to combine resolution
options to achieve cost, technical or schedule benefits. Depending on the situation, some options may
be deemed inherently more feasible or appropriate by the analyst, and this
determination may have the potential to affect the degree to which each solution
is investigated. Nonetheless, in each
case the analyst should ensure a baseline evaluation of all available resolution
options in order to facilitate comprehensive resolution
analyses.
AfterMarket
Obsolete parts can often be obtained from aftermarket
manufacturers and brokers. These
companies buy entire production lines, with manufacturing rights, for parts from
the original manufacturers. Some
aftermarket companies have ongoing agreements with the big manufacturers for the
first chance at buying production lines about to be closed down. Aftermarket manufacturers are a good source
for reliable parts, since the process and materials are the same. Many OEMs have established routine transfer
agreements with aftermarket activities for discontinued product line
support. Unfortunately, these parts can
be significantly more expensive than those offered by the original
manufacturer. The aftermarket supplier
has smaller production runs, and must recoup his initial costs of buying the
line and setting it up.
Reclamation
This alternative should be considered primarily to resolve
crisis DMSMS situations, as a short-term resolution alternative, or in cases
where remaining LOT demand is minimal. It will be most effective when a supply
of end items has been identified and resources are available for recovery,
testing, repackaging and storage. Potential sources for this alternative include
Beyond Economical Repair (BER) equipment at depot repair facilities; surplus and
stored material removed due to modernization programs; or items resident within
deactivated or decommissioned units. Reclamation does work as a resolution
occasionally.
Emulation
Emulation is the process of developing Form-Fit-Functional (FFF)
replacements for obsolete microcircuits using state of the art material design
and processing techniques. Emulated items
are not intended to be substitutes, but rather valid alternate parts for the
non-available components; however, a risk does exist in that emulated parts may
fail to meet certain unspecified performance characteristics of the original
item, and thus suitability for all applications may not be guaranteed. As with aftermarket manufacturers, price per
unit for emulated items is likely to be extremely sensitive to order quantities,
and the analyst must consider this fact developing a procurement strategy for
this alternative. At the same time, the
emulation process involves creation of a design library supporting wafer
fabrication; therefore, if the DMSMS item is a common or previously emulated
design, preliminary engineering costs may be greatly reduced. The emulation process may be conducted at the
IC, circuit card, or other designated system indenture level, and often
considered a subset of redesign initiatives.
GEM
Generalized
Emulation of Microcircuits (GEM) technology provides the capability to
manufacture military quality microcircuits, in small quantities, of older
technologies such as RTL, DTL, TTL, NMOS, CMOS, etc., using modern technology
and fabrication methods. That means if
you need a handful of ancient technology, obsolete microcircuits in a hurry, the
GEM can be an attractive solution.
Prototype microcircuits are generally delivered in ninety days from data
sheets, military slash sheets, source control drawings, or other custom
specifications.
VHDL
A
vendor independent data specification for microcircuits is potentially the best
approach for solving the DMS problems in military electronics. Most of
components designed today are for specific applications, eliminating the
possibility for finding a direct substitute.
Each of these high-density components is designed to perform unique
functions specific to
that single board or application.
This virtually ensures that there will not be a directly replaceable
substitute when this part becomes obsolete.
This creates two extremely critical DMS problems: (1) Since these devices
are typically complex, those without appropriate documentation (very common in
military systems) are very difficult and costly to reverse engineer. (2) If the
functions are known, but not in vendor independent format, a considerable amount
of engineering time and cost will be incurred developing a solution. To
alleviate these problems, Very High Speed Integrated Circuit Hardware
Description Language (VHDL), which allows the vendor-independent attributes can
be design solution choice for the long-term support of digital Application
Specific Integrated Circuits (ASICs).
VHDL is a computer
programming language that has been designed and optimized for describing the
functionality of digital circuits and systems.
Once a system is described in VHDL, its functionality can be identically
recreated in a different technology through computer automation. Designs ranging from simple gates to complex
functions can be “described” in VHDL.
The designer retains the flexibility to write code for specific
implementations, or for the more abstract “behavioral” level. Advanced synthesis tools are applied to
convert the vendor-independent design descriptions to vendor-specific data files
for silicon fabrication. For example, the first computer was implemented with
vacuum tubes and discrete wires. If this
first computer had been described in VHDL, its exact same functionality could be
easily and inexpensively recreated in today’s technology (integrated circuits on
a printed-wire circuit board) instead of the original technology (tubes and
discrete wires). VHDL is a potential
solution to the Diminishing Manufacturing Sources and Materiel Shortages (DMSMS)
problem because it will allow today’s systems to be easily and inexpensively
recreated through computer automation in tomorrow’s technologies when its
components become obsolete.
Redesign
It is another DMSMS solution, but requires the biggest effort
with the highest cost. Redesign is where
the engineers redesign a piece of the affected equipment or the entire
equipment, to either design the obsolete part out, or accommodate a new part (a
new technology part or same technology, different part). Redesigns are often the most expensive
solution, costing millions of dollars for design work, modifications to fielded
and production systems, changes to technical data, training material and models,
and on and on. Sometimes a redesign is
the best choice for the affected equipment as a whole. Older equipment becomes so full of near
obsolete or obsolete parts that DMSMS management is no longer cost effective and
the equipment should be redesigned or even replaced. In addition, redesign is often the favorite
solution of the Original Equipment Manufacturer since it brings more profit to
the company, where an alternate part solution means only a small change for the
company.
New Sourcing
Development of new sources for DMSMS items may be considered
when a complete reprocurement technical data package is owned or purchased by
the government. This option may be
appropriate when the DMSMS problem occurs at either the equipment or component
level, and the LOT demand is projected to be high. Developing new sources for the part is a
viable option, but often may not solve the immediate problems. Developing a new source takes time. Modifying a production line, getting the part
to turn out reliably, finding enough customers to generate a profit, testing the
part to meet performance standards, are just some of the hurdles a manufacturer
must jump to produce parts.
Reverse Engineering
Development of replicas of candidate items is accomplished
through review of available technical data and physical disassembly and analysis
of item components. When a part is
obsolete, there are no others available, even closely related parts to choose
from, and the technical data package is incomplete or nonexistent, then that
part is dissected and a new data package is recreated. That package can then be taken to industry
for competitive bidding. This process is
usually undertaken as an extreme measure, and mostly for mechanical parts. This option traditionally has been expensive
and takes a long time.
Life Of
Type Buy (LOT)
This option involves purchasing a supply of DMSMS items to
support total demands for the life of impacted systems/equipment. Based on the
procurement quantities, it can be classified into several categories of
buys. Life of Type Buy, Extended Buy, or
Bridge Buy. The concept is to make one last big buy of an item before the
manufacturer ceases production. The
amount purchased depends on whether enough stock is being bought to cover all
requirements for the remaining life of the equipment, or just enough to last
until another solution comes on line (Bridge Buy). This type of quick, large quantity buy,
especially a Life of Type Buy, seems on the surface to be a fast and easy way
out of a DMSMS problem. However, there
are some hidden pitfalls, especially if you have to support your equipment for
many years to come. Calculating how many
items to buy, especially over a period of ten or more years, is very difficult
at best. Operation tempo changes
constantly, so usage will fluctuate from year to year. The number of platforms in service changes
over time, so that if a program manager buys twenty years of stock and then the
number of active platforms is halved, he suddenly has forty years of stock on
hand. Also, during that twenty year
period of time, the equipment will usually be modified and upgraded so many
times, that the part will probably be designed right out of the equipment, and
therefore all those items in storage will be useless. Storage of items can be expensive, especially
for long periods in specialized environments.
In addition, items purchased may not have as long a shelf life as
expected. Many of the new technology
items haven’t been in existence long enough for us to know what their useful
shelf life is. This is especially true
of microelectronics. A finished part is
not the only thing that can be purchased.
Microelectronics die is a good example of an item that can be stored for
long periods, and as needed, sent to a fabrication shop for final
assembly.
LIST OF DMSMS RELATED DOCUMENTS
a. NAVSUP INSTRUCTION 4800.6
(Dated 26 February1985) Diminishing Manufacturing
sources and material shortages (DMSMS) program
b. Department of Defense Material
Management Regulation (4140.1-R)
c. DMS Case Resolution Procedure
Guide (Prepared by Naval Sea Systems Command – NAVSEA
0416)
d. Flexible
Sustainment Guide (Dated 14 August 1997) (Joint Logistics Commanders - Joint Aeronautical
Commanders’ Group)
e. Acquisition Practice for Parts Management (MIL-HDBK-965)
f. Guidelines
for the Implementation of the DOD Parts Control Program (MIL_HDBK-402A)
LIST OF DMSMS RELATED INTERNET WEBSITES
a. DMS Technology
Center (DTC): http://dtc-dms.crane.navy.mil/dtc.htm
b.
Government-Industry Data Exchange Program (GIDEP): http://www.gidep.org/
c. Defense
Microelectronics Activity (DMEA): http://www.dmea.osd.mil
d. G-12 DMSMS
Website: http://smaplab.ri.uah.edu/SMAP-CENTER/Conferences/dmsms2K/papers/hatch.pdf