Introduction
Micro-electro-mechanical
systems (MEMS) is one of the fastest growing and most promising electronics
technologies. Using existing integrated
circuit chip fabrication processes to manufacture micro-scale embedded
electrical, mechanical, and optical systems opens the door to many different
commercial and military applications.
The military, through the Defense Advanced Research Projects Agency
(DARPA), has led the way in developing this technology and bringing it close to
mass commercialization. MEMS are already
being used in automobile air bag crash sensors, ink jet printers, and NASA’s
Mars Microprobe. Many military systems
are being investigated for their potential for MEMS insertion to realize cost,
weight, and performance benefits.
Background
MEMS technology is developed
using current microelectronics manufacturing processes and materials to produce
embedded, integrated electrical, mechanical, and optical systems all on one
integrated circuit. The four basic
components of MEMS are microsensors, microactuators, microelectronics, and
microstructures. Current technology can
produce a single integrated circuit package that has micro-pumps, valves, and
switches along with the necessary electronic components to intelligently control
them. The goal of MEMS technology is to
integrate sensors that merge mechanical, optical, acoustic, and fluidic elements
with electronics to create microsystems that can sense, commute, act and
communicate [OUSD/A&T Report, Dec 97].
Originally the National Science
Foundation (NSF) funded the MEMS research through a few universities. But more recently, DARPA has been the driving
force behind MEMS technology development with significantly more funding to many
universities. As the technology has
matured over the years, industry has become involved and began participating in
applied research projects. These applied
research projects have led to the development of commercialized products, items
such as automobile air bag crash sensors and ink jet
printers.
The present market for MEMS is
primarily in pressure and inertial sensors and inkjet print heads. The pressure and inertial sensor market is
growing, while the fluidic sensors are in their infancy. The current MEMS can sense, but having them
physically act (actuators) based on the sensing is not heavily commercialized to
date.
The following is a list of military
applications that are currently being investigated:
- Inertial
systems for munitions guidance
- Unattended, low power,
wireless sensors
- Weapons safing, arming, and
fuzing
- Mass data storage devices
-
Condition-based maintenance
- Chemical/Biological agent
detection
- Aircraft aerodynamic control
-
Engine and propulsion control
MEMS technology is extremely
important to the military. MEMS is being
investigated for its insertion into legacy system applications as well as new
applications. The potential for cost and
weight reductions and performance improvements is significant. Comparison of a standard inertial measurement
unit (IMU) with a MEMS unit:
|
Conventional |
MEMS |
Mass |
1587.5 grams |
10 grams |
Size |
15 cm x 8 cm x 5 cm |
2 cm x 2 cm x 0.5 cm |
Power |
35 W |
~ 1 mw |
Survivability |
35 g’s |
100,000 g’s |
Cost
|
$20K |
$500 |
The automobile industry
realized the cost, weight and performance value in implementing MEMS
accelerometers in air bag crash systems.
The auto industry replaced a conventional $50 sensor and control system
with a $5 MEMS version of an integrated sensor and control system that had
better performance and higher reliability.
Crane’s Role
Currently, Crane is performing
contract management for a DARPA project that contains MEMS investigations as a
part of the research. Crane will develop
a test plan and conduct testing on the MEMS accelerometers, and develop a paper
that can be presented at a variety of MEMS
conferences.
Crane is also trying to 1)
identify MEMS problems that need addressed, 2) identify funds for additional
commercial MEMS component procurement and test labor to evaluate the problems,
and 3) identify and evaluate potential military applications. The testing and report generation on problem
and opportunity areas of MEMS is key to building Crane’s credibility within the
MEMS community.
Crane participated in the
kick-off meeting of the Indiana Microsystems Commercialization Consortium in
February 2001. This consortium is a
group of industry, government, and academia whose purpose is to identify and
commercialize MEMS technology applications.
The first commercial application brought to the consortium is a Honeywell
aircraft landing gear sensor system.
Crane is ramping up in MEMS
knowledge and expertise for two reasons:
1)
MEMS is recognized as a large growth area in military microelectronics
based systems
2)
Microelectronics is a Crane Core Equity
Crane’s role is to provide
customers expertise in engineering analysis and testing of MEMS related to
packaging, performance, and application suitability. Crane will provide engineering and test
services to customers with MEMS applications.
Crane will leverage off our existing microelectronics packaging expertise
to address MEMS packaging, which is one of the most prominent problems with
MEMS.
Issues &
Concerns
-
Identifying potential on-center customers that can provide the
seed funding for developing this Crane capability.
-
Development of the MEMS
technologist.
-
“Breaking in” to the MEMS arena with something substantial to
offer.
Informational
References
Special Technology Area Review On
Micro-Opto-Electro-Mechanical-Systems, Office of the Under Secretary of
Defense (Acquisition and Technology), December
1997.
Microelectromechanical Systems
Opportunities, Department of Defense, December
1995.
Maluf, Nadim. An
Introduction to Microelectromechanical Systems Engineering. Artech House. 2000.
http://web-ext2.darpa.mil/MTO/MEMS/index.html
http://mems.sandia.gov
http://mems.ida.org
http://mems.isi.edu
Images
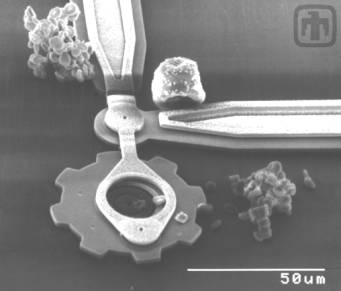
Gear Assembly. Note the single grain of pollen (right) and
the two lumps of coagulated red blood cells (upper left & lower
right).
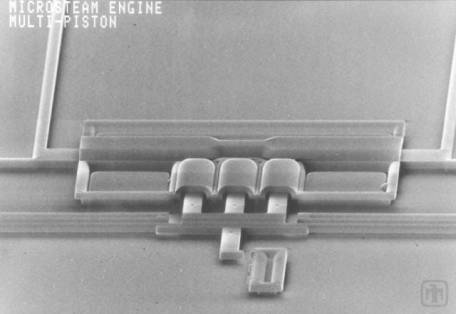
3
cylinder steam engine. The width of
the engine is less than the width of a human
hair.