Commercial passive parts are defined here as
any non-Mil-Spec or non-Mil-drawing part.
Since commercial applications are so varied, the type and quality of
commercial passive parts also vary.
Product offerings typically include consumer, industrial, automotive and
medical grades. The quality/reliability
level between the commercial grades can vary considerably as can the cost and
availability. In general, passive
suppliers do not recommend consumer grade passive parts for high-reliability
military applications. On the other end
of the spectrum, many vendors claim the parts they supply to the medical
industry are as good as if not better than Mil.
Some very good test/screening methods have come out of high-end
commercial product lines.
Commercial passives can offer significant
advantages in size, cost and availability.
Many are available in extended ranges of value and rating. These
characteristics offer obvious advantages to circuit designers where high
performance, size and weight are concerns.
Many, but not all, COTS passives are built on the same manufacturing
lines with the same raw materials as military parts. However, they tend to have less lot
traceability and pedigree is more difficult to acquire with commercial. Cost is the other significant advantage for
commercial-grade passives. Cost
differential between military and commercial parts range from 5X to 100X. And while the cost of commercial continues to
come down, as competition is always a factor, reduction in the use of military
parts has frozen or increased their cost.
This reduction in use also increases the risk of part obsolescence.
Commercial passives are a good fit for many
military applications however it is important to understand some of the
significant differences between the product lines. In general, much less testing is performed on
commercial product. This can be
particularly prohibitive in the area of screening tests such as burn-in, which
is rarely done on commercial-grade passive parts. Supplier selection becomes even more critical
since no approved source lists exist as in the military. Dependent upon the product sector, quality
variations between suppliers can be significant. Quality indicators such as ISO are important
to watch for when selecting sources. One
of the most common mistakes made by OEM’s is making source selection based
primarily on cost and delivery while leaving out a good technical assessment of
the supplier’s quality rating. Component
engineering as a part of new equipment design is much more relevant than ever
before. The parts management programs
used on military programs in the past, though somewhat outdated, are essential
in some form in order to make good decisions about part and source
selection. In general, there are fewer
passive component suppliers than there once were. Consolidation in this market sector has been
significant in the last several years.
Reduction in the number of suppliers has been even more acute in military
parts since there are not only fewer suppliers but many previous approved
sources have discontinued their military approvals. Many suppliers are now also manufacturing
part or all of their products off shore.
This is also true with military parts since there is no longer a
prohibition on offshore JAN production.
The passive industry is undergoing significant
technological change, particularly in the capacitor area. Both ceramic electrostatics and tantalum and
aluminum electrolytics are experiencing significant changes in materials and
manufacturing processes. These new
product technologies are not making their way into military product lines. Reliability testing, which has traditionally
been performed for military products and has benefited the commercial
equivalents, is no longer performed.
This leaves reliability demonstration for the new technologies up to the
manufacturer, or to field experience.
Neither of these methods should be considered good enough for mission
critical, high-reliability military applications. Having good knowledge of and a good working
relationship with the passive part suppliers is an essential prerequisite to
having quality passive parts that perform acceptably in military
applications.
Another significant change that is occurring
not only in passive components, but across the commercial electronics industry
is lead-free solder systems. Passive
manufacturers are either converting or have converted the terminations of their
commercial products to lead-free. In
most cases the solderable terminations are pure tin. Use of pure tin re-introduces the potential
for electrically conductive, tin whisker growth. This failure mode has been responsible for
the loss of millions of dollars worth of military and aerospace hardware. Lead-free alternatives to pure tin are few
and usually require significantly higher soldering temperatures. This raises yet another issue with potential
of thermal damage to sensitive components.
Acceptance of commercial
passives for military systems is completely dependent on the application and
expected performance. Non-mission
critical, environmentally benign Mil applications are a good fit for COTS
passives. Mil or space level passives
continue to be best for high reliability and/or environmentally severe
applications. All applications in
between depend on performance and reliability expectations of the
system.
POC:
NSWC Crane
Div.
Ph. 812-854-2385
PASSIVE PART
SUGGESTIONS:
·
Choose vendors and part
grades to meet the application. Look for
ISO9000 certification for vendors, and check into the level of part quality
screening performed on the parts being considered.
·
Non-hermetic plastic
packaging is used extensively by both military and commercial grade suppliers,
but reliability in general has been good.
Hermeticity is usually available only in leaded packages, not surface
mount.
·
Full-military spec parts
cost 5x to 100x that of comparable commercial-grade parts. Use them only when requirements
indicate.
·
Most
suppliers focus on commercial-grade passive parts. Selecting a different grade
(high-reliability, or military spec) may lead to increased component
obsolescence issues.
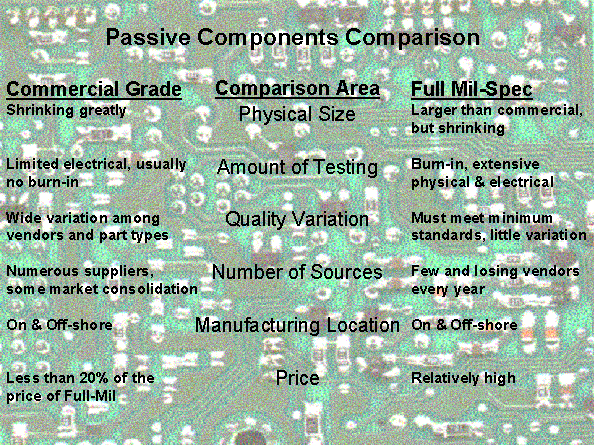