A thermistor is a specialized resistor,
intentionally designed to be thermally sensitive and its primary characteristic
is its ability to alter its electrical
resistance in response to changes in case temperature. It can be used to measure temperature, or to
sense temperature changes and compensate for the temperature changes. Thermistor resistance is a function of its
absolute temperature. Thermistors are normally available with accuracy up to
±1oC, however, higher accuracy devices are available, but
are substantially more expensive. A time constant characteristic is also
specified to signify the response rate to a temperature change (i.e., speed of
the thermistor) and is usually expressed in seconds, defined as the time
required to change 63.2% of the total difference between initial and final body
temperature, when subjected to a step function change in temperature, under
zero-power conditions. The generic
relationship between thermistor resistance and temperature is expressed in the
equation*:
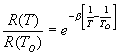
where:
R(T) = Resistance at some temperature (in
oK);
R(To)
=
Resistance at an initial measurement (reference) temperature, T (in
oK);
b =
Dissipation or thermistor material constant (usually expressed in
mW/oC or the amount of power required to induce a temperature rise of
1oC).
*Note: Some
thermistors will exhibit more complex resistance-temperature characteristics,
and it will be necessary to use a more complex form of the above equation
(usually a polynomial) to derive accurate temperature measurements. These formulas are available from the
thermistor vendor. No thermistor
exhibits linear resistance-temperature properties and in fact, most are
extremely non-linear, but it is possible to assume linearity if measurements are
made over a sufficiently small temperature range.
Packaging
Thermistors are available in several package
types. The most common package is a
disk, although they are also available with axial leads and can be purchased as
chip or Metal Electrode Leadless Faces (MELF) components for surface mount
applications. Selection of packaging
style depends on the application and where the temperature measurement needs to
be made. Surface mounted chip
thermistors will only be able to measure the temperature very close to the
board, while disk styles can be mounted at a substantial distance above the
board if the airflow needs to be sampled.
Thermistors are also available as temperature probes for specialized
applications.
Failure Mechanisms and Anomalies
Table 1.
Normalized Failure Mode Distributions for Thermistors
Failure Mode
|
Relative
Probability
|
Open
|
63%
|
Parameter
Change
|
22%
|
Short
|
15%
|
|
The most common failure mode
of a thermistor is an open circuit, as shown in Table 1. The cause of such failures
are usually due to mechanical separation between the resistor element and the
lead material, caused by handling damage, excessive heat, thermal mismatch,
etc. The second most common failure mode
is drift in resistance value as the thermistor ages, or parameter change. This results in inaccurate temperature
measurements, thereby causing the thermistor circuit to provide incorrect
thermal compensation as it ages. A short circuit is the least common failure
mode, but it is important to note that a thermistor is much more likely to fail
in the short circuit mode than a normal, fixed value resistor (by about a factor
of 3).
The unfortunate consequence of thermistor failures is
they often cause substantial secondary damage to other circuit elements when
they fail. This occurs because
thermistors are often used as protection devices against excessive heat. In addition, failure of a thermistor often
goes undiagnosed due to this secondary damage, particularly if the thermistor
fails in the parameter drift mode. For
example, one common thermistor application is to provide protection against
excessive heat in a power supply. If the
thermistor performs incorrectly, the power supply may run warmer than expected
and eventually fail. Failure is then
blamed on whatever part failed in the power supply rather than the
thermistor. The reverse can also occur,
where a protection circuit incorrectly
provides protection when it is not needed.
This results in premature shutdown.
Figure 1. Relative Failure Rates for
Thermistors
|
Reliability
|
Figure 2. Derating Requirements for
Thermistors
|
The reliability of thermistors is comparable to
wirewound resistor styles, but failure rates vary substantially with style. Figure 1 shows the relative difference between failure rates of the
three principle forms. As shown,
bead-forms are generally the most reliable and rod-forms the least.
For thermistors with negative
temperature coefficients, care must be taken to avoid thermal runaway due to
self-heating effects because it can produce permanent changes to thermistor
properties. Current limiting resistors
can help prevent thermal runaway conditions.
Derating
Derate power to 50% of maximum full rated power below
TS. Above TS,
linearly derate to TD, as shown in Figure 2,
where
.
The temperatures given in Figure 2 are for
thermistors conforming to the requirements of MIL-T-23648 (Style
RTH).
A thermistor is a mixture of metal oxides fused at high
temperature to a sintered ceramic-like semiconductor material. As previously discussed in Technologies
section, thermistors are available in four principle forms: disk, bead, rod, and
chip. The chip styles are the only ones
available with silver or gold plated terminations.
Facility Assessment
& Quality
The quality control provisions for military thermistor types
are covered through MIL-T-23648, “Thermistor (Thermally Sensitive Resistor)
Insulated, General Specification for.”
Thermistors conforming to MIL-T-23648 are required to undergo the
qualification inspections/tests given in Table 2.
Sampling
Every thermistor vendor imposes some type of sampling
plan to control the quality and uniformity of the product, but the type of
sampling will vary between vendors.
Thermistors conforming to MIL-T-23648 require sampling at specific lot
sizes and are considered nonconforming if the number of defects exceeds a given
value. Consult MIL-T-23648 to find
specific sample lot sizes and the number of allowable defects, as they are
dependent on type of test given in Table 2.
Table 2. List
of Required Qualification Tests for Thermistors Conforming to
MIL-T-23648
Visual and Mechanical
Inspection
|
Dissipating
Constant
|
Zero-Power
Resistance
|
Thermal Time
Constant
|
Resistance
Ratio
|
Terminal
Strength
|
Solderability
|
Resistance to Temperature
Characteristics
|
Resistance to
Solvents
|
Thermal
Shock
|
Short Time
Overload
|
Resistance to Soldering
Heat
|
Insulation
Resistance
|
Moisture
Resistance
|
Dielectric Withstanding
Voltage
|
Load
Life
|
Low Temperature
Storage
|
High Temperature
Exposure
|
High Temperature
Storage
|
Vibration, High
Frequency
|
Immersion
|
Shock
|
Process
Controls
The process controls of Military grade thermistors
are controlled though the requirements of MIL-T-23648. Process controls for industrial and
commercial grade thermistors will vary.
Part
Assessment
Additional qualification testing or screening by the
user is not typically performed.
Additional qualification testing or screening by the user should be left
up to the discretion of the user and is dependent on the specific
application. Qualification testing by
the user is not typically performed, although testing can be done to determine
the initial measurement reference temperature (R(To)).
Handling & Storage Precautions
Thermistor construction is very rugged, especially
for the bead-forms. Thermistors are not
considered to be ESD sensitive.
Surface mounted chip thermistors are intended to
measure temperature very close to the board.
If temperature needs to be measured at a substantial distance above the
board or if the airflow needs to be sampled, disk packages are a better choice.
The designer has the choice of three different types of devices available to
measure temperature: the resistance temperature detector (RTD), thermocouple,
and the thermistor. This section is only
applicable to the thermistor, however, to aid the designer in choosing the best
device for a given application, the following descriptions and characteristic
curves (Figure 3) are offered:
a.
The RTD is constructed similar to an
accurate wire wound resistor. It is most
accurate of the three types of temperature sensing devices because it has the
best stability and the best linear response.
Its main disadvantages are a slow response time, small resistance change,
and it is sensitive to self-heating effects.
Figure 3. Comparison
of Output Characteristics of Three Temperature Sensor
Technologies
|
b. The thermocouple is constructed with two
dis-similar metals joined together and takes advantage of the thermoelectric
potential property of dissimilar metal junctions. The main advantages of a thermocouple are
that a current source is not necessary and it has the largest temperature range
of the three types of temperature sensors.
The primary disadvantages are a low voltage (mV) output, a reference
(cold junction) temperature is needed, and it has the lowest sensitivity of the
three types.
c. The thermistor has much higher
resistance values and exhibits a larger change in resistance with respect to
temperature, but its temperature range is very limited in comparison to the
other two types of temperature
sensors.