Switches are available over a large range of different sizes,
packaging styles, and quality levels. They range from miniature pushbuttons to
large power conductors. In fact, so many switch styles are available, it is
often difficult to select the most appropriate.
Like relays, switches contain moving parts. This makes them
sensitive to wear-out failure mechanisms. Moving parts also cause switches to
have relatively high failure rates, although these high failure rates are often
due to misapplication of the part rather than inherent problems with the switch
itself. Switch selection often does not receive sufficient attention during the
design or parts selection process because switches are not considered high
priority items.
This is intended to be a guide to aid the designer in the
selection of an appropriate switch for the intended application. More detailed
information is available from vendors and MIL-STD-1132, Selection and Use of
Switches and Associated Hardware. A further source of information and complete
listings of all military specifications are available from DSCC (Defense Supply
Center Columbus) 3990 E. Broad St., Columbus, Ohio, 43216-5000.
Packaging
Switches are available in a variety of package styles,
especially among the commercial types. Many are unique to particular
applications e.g., pushbuttons, momentary tact, thumbwheel, lever types, slide
switches, rocker, key (or switchlock), toggle, rotary, DIP switches, among
others. In addition, keypads and keyboards are also considered switches. It is
beyond the scope of this document to give a detailed description of every switch
type; Table 1 and Figure 1 give an overview of
switch types.
Figure 1. Factors Affecting the Selection of
Switches
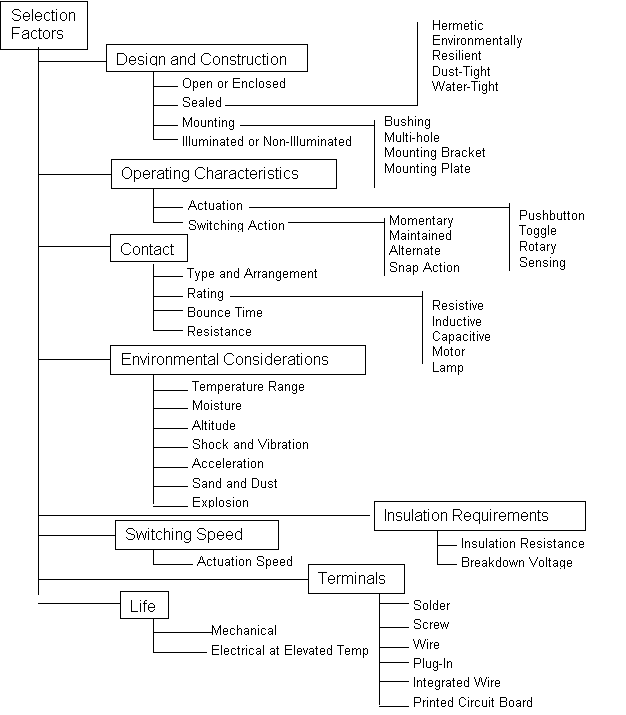
Table
1. Military Switch Styles and Applications
Switch Type
|
MIL-SPEC
|
Intended
Application
|
Switch, Push-Button,
Illuminated |
MIL-S-22885 |
Intended for panel displays
and switching devices in AC and DC applications. Panel displays include various
combinations of colors and legends. |
Switches and Switch
Assemblies, Sensitive and Push (Snap Action) |
MIL-S-8805 |
Intended for AC and DC
applications, where predetermined small and accurately controlled
characteristics are required. Various means of actuating by toggle levers, push
buttons, cams, and other light pressure devices. These switches have
snap-action, which eliminates teasing. |
Switches, Multi-Station,
push-button (Illuminated and Non-Illuminated |
MIL-S-24317 |
Intended as panel displays
and switching devices in AC and DC applications. |
Switches,
Pressure |
MIL-S-9395 |
Intended primarily to detect
changes in pressure, liquid and gas applications. |
Switches, Rotary |
MIL-S-3786 |
Intended primarily for low
power, AC or DC switching applications (capable of making and breaking a
resistive load of <2A). Includes both manually and solenoid actuated
switches. |
Switches, Rotary Selector
Power |
MIL-S-6807 |
Intended for power circuits
capable of making, arraying, and breaking electrical loads of
<10A. |
Switches, Rotary (Printed
Circuit), (Thumbwheel, Inline, and push-button) |
MIL-S-22710 |
Intended primarily for low
power AC or DC switching applications. Thumbwheel switches provide numerical or
other legend readout tied to a particular switch position. Also provided for is
logic circuitry for computer operation. |
Switches, Thermostatic
(Metallic and Bimetallic) |
MIL-S-24236 |
Intended primarily in AC and
DC applications where temperature protection or accurate temperature control or
an enclosure is required. |
Switches, Thermostatic
(Volatile Liquid), Hermetically Sealed |
MIL-S-28827 |
Intended primarily in AC and
DC applications that require rapid temperature response. |
Switches, Toggle
Environmentally Sealed |
MIL-S-3950 |
Intended where simple
make-and-break actions are required and are suitable for use on AC and DC
circuits. |
Switches, Toggle, Positive
Break |
MIL-S-8834 |
Intended in AC and DC
circuits where a positive make-and-break action is required. Positive break
actuation causes minimum contact "tease." |
Switches, Air and Liquid
Flow |
MIL-S-28788 |
Used primarily in equipment
to sense velocity and flow of air or liquid. |
Switches, Reed |
MIL-S-55433 |
Used in circuits as a
separate element where magnetically actuated, hermetically sealed switch
contacts are required. Capable of millions of operations and operations were
low-level (dry circuit) loads. |
Switches, Rotary, Snap
Action |
MIL-S-15291 |
Intended for high current
circuits capable of making and breaking 10 - 100 A at 120-150 VDC and 125-150
VAC. |
Switch enclosure methods can be divided into three
types:
a. Open Package: A package in which no effort is made to protect
the switch or its parts from atmospheric conditions
b. Environmentally Sealed or Resilient Package: The switch is
contained within a completely sealed case where there is a seal of resilient
material (e.g., gasket or seal) protecting the switch from the ingression of the
outside environment. This type of package offers increased resilience over an
enclosed package.
c. Hermetically Sealed Package: The switch is contained within a
package sealed by a process that involves fusing or soldering, and does not use
gaskets. It provides protection against the ingression of moisture, gasses, and
other harmful particulate.
Switch mounting is of four general types: (1) bushing, (2)
multi-hole, (3) mounting bracket, and (4) mounting plate. Terminals are of six
general types: (1) solder, (2) screw, (3) wire, (4) plug in, (5) integrated
wire, and (6) printed circuit board termination. The choice of mounting is
dependent on the particular application.
Switch packages are also classified by several miscellaneous
categories. For example, many types of push button switches are available in
illuminated and non-illuminated styles. Furthermore, some packages are
classified as "explosion-proof," meaning they are intended for environments
where volatile gasses surround the switch where a spark could cause an
explosion.
Failure Mechanisms and Anomalies
Table 2. Normalized Failure
Mode Distributions for Switches
|
Switch
Type
|
Failure Mode
|
Open
|
Short
|
Sticking
|
Parameter Change
|
No Control
|
Pushbutton
|
60%
|
7%
|
|
33%
|
|
Toggle
|
|
65%
|
16%
|
19%
|
|
Thermal
|
|
27%
|
2%
|
63%
|
8%
|
Failure modes of switches are
heavily dependent on the particular design of the switch, although some
generalizations can be made. Table 2 divides switches into three general
categories and gives particular failure modes of each. However, care should be exercised when using
this table because intricacies of a particular design will affect the
result. For example, the failure modes
of a heavy ruggedized switch differs substantially from the failure modes of a
momentary action plastic switch.
Unlike most other electrical parts, switches contain mechanical
elements and are therefore subject to failure mechanisms associated with
mechanical wear of the switching elements. In addition, many switches contain
spring mechanisms (especially in momentary action switches) that will lose
resiliency with age. Therefore, switches do not follow a constant hazard
(failure) rate or traditional "bathtub curve" profile. Instead, failure rates
tend to increase with age. Early life failures of switches are often caused by
contamination. Mechanical contamination creates shorts or physically blocks the
movement of mechanical elements. Non-metallic or corrosive gaseous contamination
creates open circuits by forming a surface film or oxidation on the contacts to
create an insulative barrier. Except for special high voltage and high
temperature applications, solid-state switches are inherently more reliable and
predictable for long life applications.
Reliability
From a reliability point of view, switches and relays are very
similar devices and suffer from many of the same reliability problems. Most of
the poor design practices for relays are also applicable for
switches.
Switches are considered relatively high failure rate items due
to the moving parts and the wear-out mechanisms. Vendors often specify switch
reliability by giving a maximum number of switching sequences rather than a rate
of failure with time. Reliability is further decreased as temperature rises and
adverse chemical reactions from internal materials are accelerated. In addition,
the insulation resistance between the switch contacts and ground decreases as
the temperature rises. High temperature can also affect the insulation from the
standpoint of voltage breakdown, due to a change in dielectric strength. At the
opposite extreme, switch reliability can be degraded by low temperatures. Low
temperatures can cause material contraction and cracking, allowing foreign
material and moisture to enter resulting in short circuits voltage breakdowns,
and corona arcing.
Moisture ingression has an adverse affect on reliability as
moisture in the dielectric decreases the dielectric strength, life, and
insulation resistance of the switch. It can also cause corrosion by increasing
the galvanic action between dissimilar metals in the switch. Switches that need
to give a long life in high humidity environments should therefore be
hermetically sealed. An alternative approach is to use boots, "O" rings, or
diaphragms over switch openings to decrease moisture entry.
For airborne applications, flashover becomes a problem at low
barometric pressures (see Connectors). This is particularly true of small
switches because they have smaller contact spacings. Flashover causes the switch
to momentarily engage while in the "off" position, and will decrease life if the
flashover occurs continuously. Care must be used when selecting a switch that
will operate at low barometric pressures.
Derating
Derating of continuous current depends on load type, as shown in Table 3. Derating is more
severe for inductive loads due to high current demands upon initial startup and
increased probability of voltage spikes.
Some switch specifications will contain individual current
limitations for capacitive, inductive, motor, and filament loads. For such
specifications, limit current to either the current derived from Table 3 or the maximum current
rating for the particular load type given in the specification, whichever is
less.
Table 3. Derating Requirements for
Switches
|
|
|
%
of Max Rated Value of Resistive Load in Environment
|
Part
Type
|
Derating
Parameter
|
Category 1 Protected
|
Category 2 Normal
|
Category 3 Severe
|
Switch
Non-MMIC
|
Contact Current (Continuos)
|
70--Capacitive Load
70 -- Resistive Load
50 -- Inductive Load
30
-- Motor
20 -- Filament
(Lamp)
|
60 -- Capacitive Load
60 -- Resistive Load
40 -- Inductive Load
20 -- Motor
10 -- Filament (Lamp)
|
50 -- Capacitive Load
50
-- Resistive Load
30 -- Inductive Load
20
-- Motor
10 -- Filament
(Lamp)
|
|
Contact Power
|
70
|
60
|
50
|
|
Contact Current (Surge)
|
80
|
80
|
80
|
Limit maximum power dissipation as shown in Table 3.
Where surge current is of concern, limit surge current to 80% of
maximum rated. If surge current is of concern and the switch has no a surge
current rating, it should not be used without consulting the manufacturer.
For Monolithic Microwave Integrated Circuit (MMIC) switches,
derate according to Table 4.
Table 4. Derating Requirements for MMIC
Switches
|
|
|
|
Maximum Allowable Rating in
Environment
|
Part
Type
|
Derating
Parameter
|
Rec. Max.
Value
|
Category 1
Protected
|
Category 2
Normal
|
Category 3
Severe
|
Switch
MMIC |
RF Input
Power
Control Voltage
Operating Temp
Storage
Temp
|
Mfr. Rec.
max.
-8V
125°C
-65°C to 150°C
|
100%
90%
70°C>
|
95%
80%
85°C
|
90%
70%
125°C
|
Design and Material
Controls on the materials and processes used to
manufacture switches are reflected in performance parameters. Requirements on
specific materials and processes are not generally specified in specifications
with the exception of interface requirements such as size, mass, lead plating,
etc. To obtain further information on the material and baseline-design controls,
contact the vendor, consult MIL-STD-1182, or examine an individual military
specification listed in Table 1.
Facility Assessment and Quality
Nearly every type of switch is available in a wide
range of quality levels. Numerically, quality can be specified by operating
life, which is given as the number of switch cycles before wear-out. Switch
cycles normally range from 50,000 to 1 million, which vendors consider the
guaranteed minimum number of cycles the switch can withstand under normal
operating conditions before failure. Quality is further dependent on the
ruggedness of the package and how well the internal switching elements are
sealed against influences of the outside environment. Selecting commercial grade
switches or switches used on COTS hardware for Military applications is not
recommended unless there is assurance the switch will operate for the extended
lifetime and typically harsher environmental conditions of Military
hardware.
Some vendors will advertise they are ISO 9000 quality
certified or have an ISO 9000 quality system in place. This means that the
vendor has a disciplined quality system in place, but it does not necessarily
mean the switches produced will operate reliably in the harsh conditions of a
Military environment. Attention must also be paid to the design of the
switch.
Sampling
Sampling plans of switches constructed to Military
specifications are specified within the Military specifications listed in Table 1, although the current
trend in the military specifications is away from calling out specific sample
sizes and towards end item performance requirements. If the user needs to know
the quality control sample size used during manufacturing, consult the
individual vendor.
Process Controls
The user needs to know the process controls and SPC
used during the manufacturing operation; the manufacturer should be consulted.
The military specifications for switches, listed in Table 1, contain process
control requirements, but each specification is different and the current trend
is to move away from process control requirements and towards end item
performance requirements.
Part Assessment
No additional testing, qualification, screening, or
conditioning is normally required of the manufacturer at the part
level.
Handling and Storage Precautions
Switches require only normal handling precautions as
they are not considered Electrostatic Discharge (ESD) sensitive.
Switches should never be placed in parallel
redundancy for increasing the current handling capability of a circuit. Parallel
redundancy should only be used for switches when each switch can sufficiently
handle the current carrying requirements of the circuit.
Switches used in digital circuits should be carefully
reviewed to assure contact bounce (or chatter) will not be incorrectly
interpreted and result in logic errors. Further, the designer should take into
account that contact bounce and settling time will increase with age.
High vibration and shock environments of many
Military applications, particularly airborne, may cause contact chatter. Such
environments may dictate the use of solid state devices, or special mounting
methods may be used to minimize vibration and shock amplification. For high
vibration and shock environments, the maximum anticipated vibrational
acceleration should remain less than 75% of the maximum rated acceleration the
switch is rated to withstand.
DIP switches are mounted directly to printed wiring
boards and are used to initialize settings or configurations. DIP switches are
discouraged on Military hardware due to propensity of the switch to contain
incorrect settings and lack of documentation in fielded conditions.
Some switch devices do not specify a surge current
rating. Recommend such devices not be used if surge current is of concern, as,
generally, these devices are not designed to handle surge
currents.